Editor’s Note: Take a look at our featured best practice, TWI Program: Job Safety (JS) Training (104-slide PowerPoint presentation). Based on the TWI instructional model, the Job Safety (JS) program creates a simple and logical framework by which supervisors can prevent accidents from happening by learning how to analyze the causes of accidents and eliminating them before they happen. In addition to physical causes, JS [read more]
* * * *
Workplace safety is a critical priority across all industries, but the reality is that no two sectors face the same risks. What works for a warehouse environment may be completely unsuitable for a healthcare facility or a manufacturing plant. That’s why tailoring your safety program to the specific needs of your industry is essential for protecting employees, maintaining compliance, and promoting operational efficiency.
In this blog, we’ll explore how you can create an effective, industry-specific safety program that truly meets your workplace’s unique demands.
Use Industry-Appropriate Signage and Communication
Clear, relevant communication plays a vital role in any safety program. Safety signage is a practical, visual way to reinforce protocols and alert employees to specific risks. Different industries require different types of signage. For example, chemical plants use specialized hazard signs indicating toxic substances and protective zones, whereas construction sites benefit from clear warnings about heavy equipment and fall risks.
It’s important to invest in signage designed specifically for your workplace environment to maximize its impact. For expert signage solutions that cater to various industries, you can go here to explore a wide range of workplace safety products. Incorporating the right signage helps keep safety top of mind and reduces accidents caused by misunderstandings or lack of awareness.
Understand Your Industry’s Unique Hazards
The foundation of any tailored safety program lies in a deep understanding of the particular hazards your industry presents. For instance, construction companies commonly grapple with fall hazards, heavy equipment accidents, and electrical risks. Meanwhile, food processing plants need to focus on contamination control and machinery safety, while offices prioritize ergonomics and fire evacuation plans.
Begin by conducting a comprehensive risk assessment involving employees, safety officers, and management. This helps identify the precise risks workers face daily. The assessment should cover everything from common accidents to less obvious threats like chemical exposures or repetitive strain injuries. Knowing the specific dangers enables you to concentrate safety efforts where they are most needed rather than using a broad, generic approach.
Align Your Safety Program with Industry Regulations
Compliance with health and safety regulations is not only a legal obligation but also a practical necessity for tailored safety programs. Different industries are subject to varied laws and standards. For example, healthcare facilities must comply with infection control protocols and biological hazard management. In contrast, manufacturing sectors must follow strict machinery safety and personal protective equipment (PPE) guidelines.
Stay up to date with relevant regulations from bodies such as the Health and Safety Executive (HSE) in the UK or OSHA in the US. Industry associations also provide best practice frameworks that help you build a program suited to your sector. Aligning your safety initiatives with these rules ensures you meet compliance requirements and reinforces your commitment to employee safety.
Develop Role-Specific Training and Procedures
Employees in different roles encounter different hazards, so safety training must be customized accordingly. For example, warehouse workers require training on safe forklift operation and manual handling techniques, while laboratory staff need instruction on chemical handling and spill response.
Generic safety training is unlikely to be effective if it does not reflect the real tasks and risks of each job. Creating tailored training modules and regular refreshers improves employee understanding and adherence to safety practices. This approach also boosts confidence, making workers more likely to follow procedures and report hazards.
Monitor, Review, and Continuously Improve
Industries evolve, technologies advance, and workplace dynamics change — so your safety program should never be static. Regular monitoring through safety audits, inspections, and incident analyses helps identify any weaknesses or emerging risks.
Encourage employee feedback and open communication channels to capture frontline insights. Use this information to update training, refresh signage, and refine procedures. This cycle of continuous improvement ensures your program remains effective and aligned with current industry challenges.
Foster a Safety Culture Unique to Your Industry
Ultimately, the success of any safety program depends on the culture within your organization. Promoting a workplace culture where safety is ingrained in everyday activities is especially important when tailoring programs to specific industries.
Encourage all employees to take responsibility for safety by recognizing good practices, promptly reporting hazards, and participating in safety initiatives. A strong safety culture that fits your industry’s environment helps sustain long-term compliance and keeps everyone engaged in creating a safer workplace.
Tailoring your safety program to your industry’s particular needs involves understanding your unique hazards, aligning with regulations, providing role-specific training, using appropriate signage, continuously monitoring progress, and fostering the right culture. This holistic approach protects your workforce while supporting business goals and compliance.
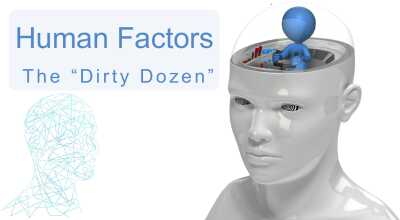
92-slide PowerPoint presentation
Various industries including aviation sector have realized the need of understating in human factors and utilization and application of the understanding in order to protect human and properties and enhance productivities [read more]
Do You Want to Implement Business Best Practices?
You can download in-depth presentations on Workplace Safety and 100s of management topics from the FlevyPro Library. FlevyPro is trusted and utilized by 1000s of management consultants and corporate executives.
For even more best practices available on Flevy, have a look at our top 100 lists:
These best practices are of the same as those leveraged by top-tier management consulting firms, like McKinsey, BCG, Bain, and Accenture. Improve the growth and efficiency of your organization by utilizing these best practice frameworks, templates, and tools. Most were developed by seasoned executives and consultants with over 20+ years of experience.
Readers of This Article Are Interested in These Resources
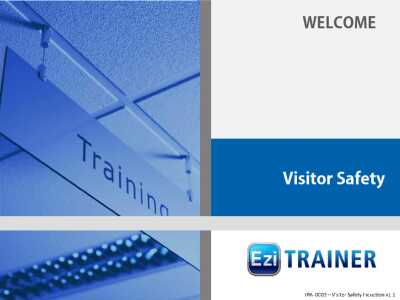
16-slide PowerPoint presentation
This Visitor Induction contains information to provide your visitors with the essential instruction and information to ensure their visit to your workplace is safe. This information [read more]
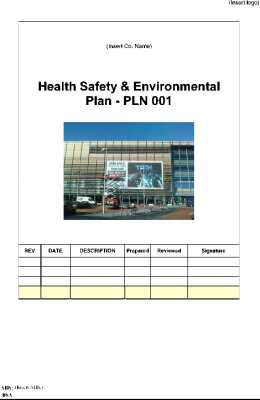
29-page Word document
The key elements include: HSE policy, risk management, management responsibilities, incident investigation, [read more]
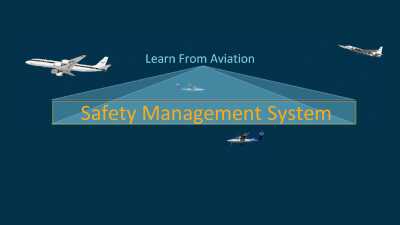
79-slide PowerPoint presentation
In an era where digital transformation sweeps across industries at an unprecedented pace, organizations must adapt swiftly to harness the power of technology. This paradigm shift, ushered in by digitalization, not only unlocks new opportunities but also redefines operations, business [read more]
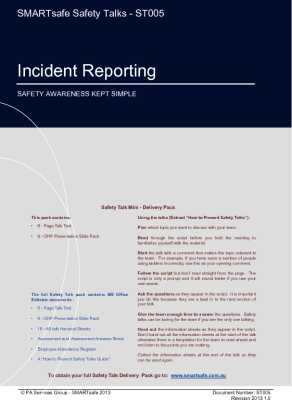
19-page PDF document